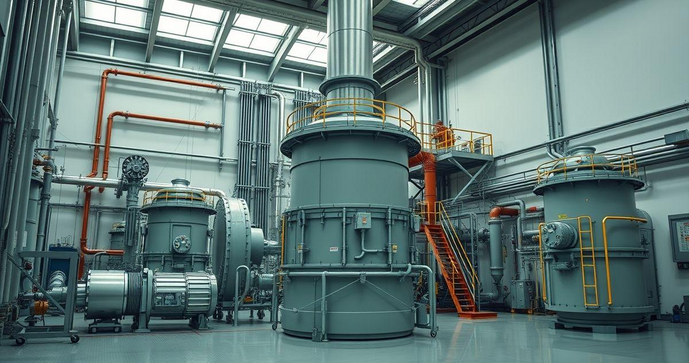
Saiba sobre Reatores Industriais: Como Escolher o Modelo Ideal para Sua Indústria
Reatores Industriais desempenham um papel crucial em diversos processos químicos e de produção, sendo fundamentais para a transformação de matérias-primas em produtos finais. A escolha do reator adequado pode impactar significativamente a eficiência, a segurança e a qualidade da produção. Neste artigo, abordaremos os diferentes tipos de reatores, fatores a serem considerados na seleção, suas vantagens e a importância da manutenção para garantir um funcionamento seguro e eficaz.
Tipos de Reatores Industriais e Suas Aplicações
Os reatores industriais são equipamentos essenciais em processos químicos, permitindo a realização de reações controladas que transformam matérias-primas em produtos finais. Existem diversos tipos de reatores, cada um projetado para atender a necessidades específicas de produção. A seguir, exploraremos os principais tipos de reatores industriais e suas aplicações em diferentes setores.
1. Reatores de Batelada
Os reatores de batelada são utilizados para realizar reações em lotes, ou seja, uma quantidade específica de matéria-prima é processada de cada vez. Este tipo de reator é ideal para processos que não exigem produção contínua e é amplamente utilizado na indústria farmacêutica, alimentícia e de cosméticos. A flexibilidade dos reatores de batelada permite a adaptação a diferentes formulações e volumes de produção, tornando-os uma escolha popular para empresas que trabalham com produtos variados.
Uma das principais vantagens dos reatores de batelada é a capacidade de realizar reações complexas que exigem condições específicas, como temperatura e pressão controladas. Além disso, eles permitem a fácil limpeza e manutenção, o que é crucial em indústrias que lidam com produtos sensíveis, como medicamentos e alimentos.
2. Reatores Contínuos
Os reatores contínuos, como o próprio nome sugere, operam de forma contínua, permitindo a entrada constante de matérias-primas e a saída contínua de produtos. Este tipo de reator é amplamente utilizado em processos de grande escala, como na produção de combustíveis, produtos químicos e plásticos. A eficiência dos reatores contínuos é uma de suas principais características, pois eles podem operar por longos períodos sem interrupções, resultando em maior produtividade.
Os reatores contínuos podem ser classificados em diferentes categorias, como reatores de fluxo tubular e reatores de leito fixo. Os reatores de fluxo tubular são ideais para reações que ocorrem rapidamente, enquanto os reatores de leito fixo são mais adequados para reações que exigem tempo de residência mais longo. A escolha do tipo de reator contínuo depende das características da reação e das propriedades dos materiais envolvidos.
3. Reatores de Leito Fluidizado
Os reatores de leito fluidizado são projetados para permitir que partículas sólidas sejam suspensas em um fluido, criando um leito fluidizado. Este tipo de reator é amplamente utilizado em processos de catálise, onde a reação ocorre na superfície das partículas sólidas. Os reatores de leito fluidizado são comuns na indústria petroquímica e na produção de fertilizantes, devido à sua eficiência em promover reações rápidas e uniformes.
A principal vantagem dos reatores de leito fluidizado é a excelente transferência de calor e massa, o que resulta em reações mais eficientes. Além disso, a facilidade de controle das condições operacionais, como temperatura e pressão, torna esses reatores uma escolha popular para processos que exigem precisão e consistência.
4. Reatores de Mistura
Os reatores de mistura são projetados para garantir uma homogeneização eficaz dos reagentes, promovendo uma reação uniforme. Este tipo de reator é amplamente utilizado em indústrias que produzem tintas, revestimentos e produtos químicos, onde a mistura adequada dos componentes é crucial para a qualidade do produto final.
Os reatores de mistura podem ser equipados com diferentes tipos de agitadores e sistemas de controle para otimizar o processo de mistura. A escolha do tipo de reator de mistura depende das propriedades dos materiais a serem processados e das exigências do produto final.
5. Reatores de Polimerização
Os reatores de polimerização são utilizados na produção de polímeros, que são materiais amplamente utilizados em diversas aplicações, desde embalagens até componentes eletrônicos. Este tipo de reator pode ser projetado para operar em batelada ou de forma contínua, dependendo do tipo de polímero a ser produzido.
A polimerização pode ocorrer por diferentes mecanismos, como polimerização por adição ou por condensação, e os reatores são projetados para atender às necessidades específicas de cada processo. A escolha do reator de polimerização é fundamental para garantir a qualidade e as propriedades do polímero final.
Além dos tipos mencionados, é importante considerar a manutenção adequada dos reatores industriais para garantir seu funcionamento eficiente e seguro. A Manutenção em trocador de calor é um exemplo de cuidado necessário para evitar falhas e prolongar a vida útil do equipamento.
Em resumo, a escolha do tipo de reator industrial adequado depende das características do processo, das propriedades dos materiais e das exigências do produto final. Compreender as diferentes opções disponíveis e suas aplicações é essencial para otimizar a produção e garantir a qualidade dos produtos químicos e industriais.
Fatores a Considerar na Escolha de Reatores Industriais
A escolha do reator industrial adequado é uma decisão crítica que pode impactar significativamente a eficiência, a segurança e a qualidade do processo produtivo. Existem diversos fatores a serem considerados ao selecionar um reator, e cada um deles desempenha um papel importante na operação e no desempenho do equipamento. A seguir, discutiremos os principais fatores que devem ser levados em conta na escolha de reatores industriais.
1. Tipo de Reação Química
O primeiro fator a ser considerado é o tipo de reação química que será realizada. As reações podem ser classificadas em diferentes categorias, como reações de adição, substituição, eliminação e polimerização. Cada tipo de reação pode exigir condições específicas, como temperatura, pressão e tempo de residência. Portanto, é fundamental entender as características da reação para escolher o reator mais adequado.
Por exemplo, reações que ocorrem rapidamente podem ser mais bem atendidas por reatores contínuos, enquanto reações que exigem um controle mais rigoroso das condições podem se beneficiar de reatores de batelada. A compreensão do mecanismo da reação e das propriedades dos reagentes é essencial para garantir a eficiência do processo.
2. Propriedades dos Materiais
As propriedades dos materiais envolvidos na reação, como viscosidade, densidade, solubilidade e reatividade, também são fatores cruciais na escolha do reator. Materiais com alta viscosidade podem exigir reatores equipados com sistemas de agitação mais robustos para garantir uma mistura adequada. Além disso, a solubilidade dos reagentes pode influenciar a escolha do tipo de reator, especialmente em processos que envolvem fases líquidas e sólidas.
Outro aspecto importante é a reatividade dos materiais. Reagentes altamente reativos podem exigir reatores projetados para suportar condições extremas, como alta pressão e temperatura, além de sistemas de segurança adicionais para evitar acidentes. Portanto, a análise das propriedades dos materiais é fundamental para garantir a segurança e a eficiência do processo.
3. Escala de Produção
A escala de produção é outro fator determinante na escolha do reator. Reatores de batelada são frequentemente utilizados em pequenas escalas de produção, onde a flexibilidade e a capacidade de realizar diferentes formulações são essenciais. Por outro lado, reatores contínuos são mais adequados para operações em larga escala, onde a eficiência e a produtividade são prioridades.
Ao considerar a escala de produção, é importante avaliar não apenas o volume de produção desejado, mas também a frequência de operação. Reatores contínuos podem ser mais vantajosos em processos que exigem produção constante, enquanto reatores de batelada podem ser mais apropriados para produtos que são fabricados em lotes ou em quantidades menores.
4. Condições Operacionais
As condições operacionais, como temperatura e pressão, são fatores críticos na escolha do reator. Cada tipo de reator tem limites específicos de operação, e é fundamental garantir que o reator escolhido possa operar dentro dessas condições. Reações que ocorrem a altas temperaturas ou pressões podem exigir reatores projetados para suportar essas condições extremas, além de sistemas de controle e monitoramento adequados.
Além disso, a escolha do material de construção do reator deve ser compatível com as condições operacionais e os reagentes utilizados. Materiais resistentes à corrosão e ao desgaste são essenciais para garantir a durabilidade e a segurança do equipamento. Portanto, a análise das condições operacionais é fundamental para evitar falhas e garantir a eficiência do processo.
5. Custo e Viabilidade Econômica
O custo do reator e a viabilidade econômica do projeto são fatores que não podem ser ignorados. A escolha do reator deve levar em consideração não apenas o custo inicial de aquisição, mas também os custos operacionais, de manutenção e de energia. Reatores mais complexos podem ter um custo inicial mais alto, mas podem oferecer maior eficiência e economia a longo prazo.
Além disso, é importante avaliar o retorno sobre o investimento (ROI) e a rentabilidade do processo. A análise econômica deve incluir uma estimativa dos custos de produção, do preço de venda do produto final e do tempo necessário para recuperar o investimento. Essa avaliação ajudará a determinar se o projeto é viável e se o reator escolhido atende às expectativas financeiras.
6. Manutenção e Suporte Técnico
A manutenção do reator é um aspecto crucial que deve ser considerado na escolha do equipamento. Reatores que exigem manutenção frequente ou complexa podem aumentar os custos operacionais e afetar a eficiência do processo. Portanto, é importante escolher reatores que sejam projetados para facilitar a manutenção e que tenham um bom suporte técnico disponível.
Além disso, a disponibilidade de peças de reposição e a assistência técnica são fatores importantes a serem considerados. Reatores de fabricantes com boa reputação e suporte técnico confiável podem oferecer maior segurança e tranquilidade ao longo da vida útil do equipamento.
Em resumo, a escolha de Reatores Industriais deve ser baseada em uma análise cuidadosa de diversos fatores, incluindo o tipo de reação, as propriedades dos materiais, a escala de produção, as condições operacionais, os custos e a manutenção. Compreender esses aspectos é fundamental para garantir a eficiência, a segurança e a qualidade do processo produtivo, resultando em produtos finais que atendam às expectativas do mercado.
Vantagens dos Reatores Industriais na Produção
Os reatores industriais são componentes essenciais em diversos processos de produção, desempenhando um papel crucial na transformação de matérias-primas em produtos finais. A escolha de um reator adequado pode trazer inúmeras vantagens, que impactam diretamente a eficiência, a segurança e a qualidade da produção. Neste artigo, exploraremos as principais vantagens dos reatores industriais e como eles contribuem para otimizar processos em diferentes setores.
1. Eficiência na Produção
Uma das principais vantagens dos reatores industriais é a eficiência que eles proporcionam nos processos de produção. Reatores bem projetados permitem que as reações químicas ocorram de maneira controlada e otimizada, resultando em maior rendimento e menor desperdício de matérias-primas. Isso é especialmente importante em indústrias que operam com margens de lucro apertadas, onde cada grama de produto conta.
Além disso, a automação dos reatores industriais permite um controle preciso das condições operacionais, como temperatura, pressão e tempo de residência. Essa automação não apenas aumenta a eficiência, mas também reduz a variabilidade do processo, garantindo que os produtos finais atendam consistentemente aos padrões de qualidade.
2. Flexibilidade de Produção
Os reatores industriais oferecem uma flexibilidade significativa na produção, permitindo que as empresas se adaptem rapidamente às mudanças nas demandas do mercado. Reatores de batelada, por exemplo, são ideais para processos que exigem a produção de diferentes produtos em quantidades variadas. Essa flexibilidade é crucial em setores como o farmacêutico e o alimentício, onde as formulações podem mudar com frequência.
Além disso, muitos reatores modernos são projetados para facilitar a troca de produtos e a limpeza, permitindo que as empresas mudem rapidamente de uma produção para outra. Essa capacidade de adaptação é uma vantagem competitiva importante em um mercado em constante evolução.
3. Melhoria na Qualidade do Produto
A qualidade do produto final é uma preocupação central em qualquer processo de produção. Os reatores industriais, quando projetados e operados corretamente, podem melhorar significativamente a qualidade dos produtos. O controle rigoroso das condições de reação, como temperatura e pressão, ajuda a garantir que as reações ocorram de maneira eficiente e que os produtos finais atendam aos padrões de qualidade exigidos.
Além disso, a utilização de reatores com sistemas de monitoramento e controle avançados permite a detecção precoce de problemas, como desvios nas condições de operação. Isso possibilita a correção imediata de falhas, minimizando o risco de produção de lotes defeituosos e garantindo a satisfação do cliente.
4. Redução de Custos Operacionais
Os reatores industriais também podem contribuir para a redução dos custos operacionais. A eficiência na utilização de matérias-primas e a minimização de desperdícios resultam em economias significativas. Além disso, a automação dos processos reduz a necessidade de intervenção manual, diminuindo os custos com mão de obra e aumentando a segurança operacional.
Outro aspecto importante é a possibilidade de otimização do consumo de energia. Reatores modernos são projetados para operar de maneira mais eficiente, consumindo menos energia durante o processo. Isso não apenas reduz os custos operacionais, mas também contribui para a sustentabilidade ambiental, um fator cada vez mais relevante nas práticas industriais.
5. Segurança Operacional
A segurança é uma preocupação primordial em qualquer instalação industrial. Os reatores industriais são projetados com uma série de recursos de segurança que ajudam a minimizar os riscos associados às reações químicas. Sistemas de controle avançados, válvulas de segurança e dispositivos de monitoramento são apenas alguns exemplos de como a segurança é integrada ao design dos reatores.
Além disso, a automação dos processos permite um monitoramento constante das condições operacionais, possibilitando a detecção precoce de anomalias e a implementação de medidas corretivas antes que se tornem problemas sérios. Isso não apenas protege os trabalhadores, mas também reduz o risco de danos ao equipamento e ao meio ambiente.
6. Integração com Outros Sistemas
Os reatores industriais podem ser facilmente integrados a outros sistemas de produção, como tanques de armazenamento e sistemas de transporte. Essa integração permite uma operação mais coesa e eficiente, onde os materiais podem ser transferidos entre diferentes etapas do processo sem interrupções. Por exemplo, a combinação de reatores com Tanques industriais facilita o armazenamento e a manipulação de produtos químicos, otimizando o fluxo de trabalho e aumentando a eficiência geral da produção.
Além disso, a integração com sistemas de automação e controle permite uma gestão mais eficaz dos processos, resultando em uma operação mais fluida e produtiva. Essa sinergia entre diferentes componentes do sistema de produção é fundamental para maximizar a eficiência e a qualidade dos produtos finais.
7. Sustentabilidade e Responsabilidade Ambiental
Por fim, os reatores industriais modernos são projetados com foco na sustentabilidade e na responsabilidade ambiental. A eficiência na utilização de matérias-primas e a redução de resíduos são aspectos fundamentais que contribuem para práticas industriais mais sustentáveis. Além disso, muitos reatores são projetados para operar com menor consumo de energia, reduzindo a pegada de carbono da produção.
A adoção de tecnologias mais limpas e eficientes não apenas atende às exigências regulatórias, mas também melhora a imagem da empresa perante os consumidores, que estão cada vez mais preocupados com a sustentabilidade. Portanto, investir em reatores industriais que promovam práticas sustentáveis é uma estratégia inteligente para o futuro.
Em resumo, as vantagens dos reatores industriais na produção são numerosas e impactam diretamente a eficiência, a qualidade e a segurança dos processos. Compreender essas vantagens é essencial para as empresas que buscam otimizar suas operações e se destacar em um mercado competitivo.
Manutenção e Segurança em Reatores Industriais
A manutenção e a segurança em reatores industriais são aspectos cruciais para garantir a eficiência operacional e a proteção dos trabalhadores e do meio ambiente. Os reatores, sendo equipamentos complexos que realizam reações químicas sob condições controladas, exigem cuidados específicos para evitar falhas e acidentes. Neste artigo, abordaremos a importância da manutenção, as melhores práticas de segurança e as medidas que podem ser adotadas para garantir a operação segura e eficiente dos reatores industriais.
1. Importância da Manutenção
A manutenção regular dos reatores industriais é fundamental para garantir seu funcionamento adequado e prolongar sua vida útil. A falta de manutenção pode levar a falhas operacionais, que podem resultar em paradas não programadas, perda de produção e até mesmo acidentes graves. Portanto, é essencial implementar um programa de manutenção preventiva que inclua inspeções regulares, limpeza e reparos conforme necessário.
Além disso, a manutenção ajuda a identificar problemas potenciais antes que se tornem críticos. Por exemplo, a verificação de componentes como válvulas, bombas e sistemas de controle pode prevenir falhas que poderiam comprometer a segurança do processo. A manutenção proativa não apenas aumenta a confiabilidade do reator, mas também contribui para a eficiência energética, reduzindo custos operacionais a longo prazo.
2. Tipos de Manutenção
Existem diferentes tipos de manutenção que podem ser aplicados aos reatores industriais, cada um com suas características e objetivos. A manutenção preventiva é a mais comum e envolve a realização de inspeções e serviços programados para evitar falhas. Isso pode incluir a troca de peças desgastadas, a lubrificação de componentes móveis e a calibração de instrumentos de medição.
A manutenção preditiva, por outro lado, utiliza tecnologias de monitoramento para prever falhas antes que ocorram. Isso pode incluir o uso de sensores para monitorar a temperatura, pressão e vibração do reator. Com essas informações, é possível identificar padrões que indicam a necessidade de manutenção antes que um problema ocorra.
Por fim, a manutenção corretiva é realizada após a ocorrência de uma falha. Embora seja inevitável em alguns casos, a manutenção corretiva deve ser minimizada, pois pode resultar em paradas inesperadas e custos elevados. Portanto, um bom programa de manutenção deve priorizar a manutenção preventiva e preditiva.
3. Segurança em Reatores Industriais
A segurança é uma preocupação primordial em qualquer instalação industrial, especialmente em reatores que lidam com substâncias químicas potencialmente perigosas. A implementação de práticas de segurança adequadas é essencial para proteger os trabalhadores e o meio ambiente. Isso inclui a adoção de normas e regulamentos de segurança, bem como a realização de treinamentos regulares para os funcionários.
Um dos principais aspectos da segurança em reatores industriais é a instalação de sistemas de controle e monitoramento. Esses sistemas permitem o acompanhamento em tempo real das condições operacionais do reator, como temperatura, pressão e níveis de reagentes. A detecção precoce de anomalias pode evitar acidentes e garantir que as operações sejam realizadas dentro dos limites seguros.
Além disso, a utilização de equipamentos de proteção individual (EPIs) é fundamental para garantir a segurança dos trabalhadores. Isso inclui o uso de luvas, óculos de proteção, respiradores e vestimentas adequadas. A conscientização sobre a importância do uso de EPIs deve ser parte integrante da cultura de segurança da empresa.
4. Treinamento e Capacitação
O treinamento e a capacitação dos funcionários são essenciais para garantir a segurança e a eficiência na operação de reatores industriais. Os trabalhadores devem ser treinados não apenas nas operações do reator, mas também nas práticas de segurança e nas medidas de emergência. Isso inclui a identificação de riscos, o uso correto de EPIs e a resposta a situações de emergência.
Além disso, simulações de situações de emergência podem ser realizadas para preparar os funcionários para lidar com possíveis acidentes. Essas simulações ajudam a garantir que todos saibam como agir em caso de vazamentos, incêndios ou outras situações críticas, minimizando os riscos e aumentando a segurança geral da operação.
5. Inspeções e Auditorias de Segurança
As inspeções regulares e as auditorias de segurança são práticas importantes para garantir que os reatores industriais estejam operando de acordo com as normas de segurança. Essas inspeções devem ser realizadas por profissionais qualificados que possam identificar possíveis riscos e recomendar melhorias. Além disso, as auditorias de segurança ajudam a garantir que as práticas de segurança estejam sendo seguidas e que os procedimentos de manutenção estejam sendo implementados corretamente.
As auditorias também podem incluir a revisão de registros de manutenção e incidentes, permitindo que a empresa identifique padrões e áreas que precisam de atenção. A implementação de um sistema de gestão de segurança pode ajudar a monitorar e melhorar continuamente as práticas de segurança na operação de reatores industriais.
6. Integração com Outros Sistemas
A integração dos reatores industriais com outros sistemas, como Evaporador industrial e tanques de armazenamento, é fundamental para otimizar a operação e garantir a segurança. Essa integração permite um fluxo contínuo de materiais e informações, facilitando a gestão do processo e melhorando a eficiência geral.
Além disso, a integração com sistemas de automação e controle pode melhorar a segurança, permitindo um monitoramento mais eficaz das condições operacionais e a implementação de medidas corretivas em tempo real. Essa abordagem integrada contribui para uma operação mais segura e eficiente, reduzindo os riscos associados ao manuseio de substâncias químicas.
Em resumo, a manutenção e a segurança em reatores industriais são aspectos fundamentais que devem ser priorizados para garantir a eficiência operacional e a proteção dos trabalhadores e do meio ambiente. A implementação de um programa de manutenção eficaz, a adoção de práticas de segurança adequadas e o treinamento contínuo dos funcionários são essenciais para minimizar riscos e garantir a operação segura e eficiente dos reatores industriais.
Em conclusão, os reatores industriais são componentes essenciais que influenciam diretamente a eficiência, a segurança e a qualidade dos processos de produção. A escolha do tipo adequado de reator, considerando fatores como o tipo de reação, as propriedades dos materiais e as condições operacionais, é fundamental para otimizar a produção e garantir a satisfação do cliente. Além disso, a manutenção regular e as práticas de segurança são cruciais para prevenir falhas e acidentes, assegurando um ambiente de trabalho seguro e produtivo. Ao investir na seleção correta e na manutenção dos reatores, as indústrias podem não apenas melhorar sua eficiência operacional, mas também contribuir para a sustentabilidade e a responsabilidade ambiental em suas operações.
Gostou? compartilhe!